Cakera pengisaran memainkan peranan penting dalam pelbagai industri, memudahkan pembentukan dan kemasan bahan. Walau bagaimanapun, seperti mana-mana alat lain, mereka tidak terlepas daripada isu yang boleh menghalang kecekapan dan prestasi mereka. Dalam artikel ini, kami akan menyelidiki isu cakera pengisaran biasa, meneroka puncanya dan menyediakan penyelesaian yang berkesan untuk aliran kerja yang lancar.
pengenalan
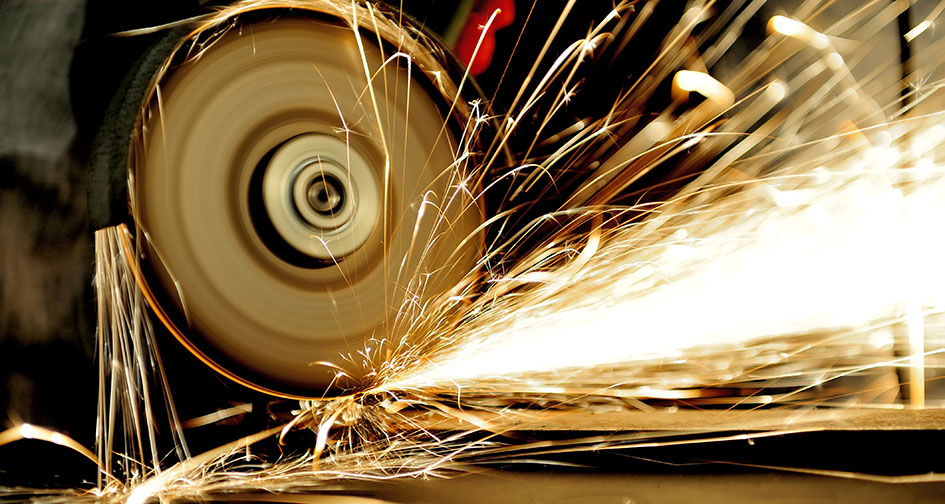
Cakera Pengisaran memainkan peranan asas dalam pelbagai industri, berfungsi sebagai alat penting untuk proses penyingkiran, pembentukan dan kemasan bahan. Memahami takrifan, kepentingan merentas industri dan isu biasa yang dihadapi adalah penting untuk mengoptimumkan penggunaannya dan memastikan operasi yang cekap.
A. Definisi Cakera Pengisaran
Cakera pengisar ialah alat pelelas yang digunakan dalam proses pemesinan untuk memotong, mengisar atau mengilat permukaan bahan. Cakera ini biasanya terdiri daripada zarah kasar yang diikat pada bahan sokongan, mencipta alat berputar yang boleh mengeluarkan bahan berlebihan, permukaan licin atau menajamkan tepi. Mereka datang dalam pelbagai bentuk dan saiz, setiap satu direka untuk aplikasi tertentu.
B. Kepentingan dalam Pelbagai Industri
Industri Kerja Logam:
Dalam fabrikasi dan pembuatan logam, cakera pengisaran adalah penting untuk membentuk, menyahburkan dan menamatkan permukaan logam. Ia biasanya digunakan dengan pengisar sudut untuk mencapai dimensi yang tepat dan kualiti permukaan.
Industri Pembinaan:
Profesional pembinaan bergantung pada cakera pengisaran untuk tugas-tugas seperti penyediaan permukaan konkrit, melicinkan tepi kasar dan menghilangkan ketidaksempurnaan dalam bahan seperti batu dan konkrit.
Industri Automotif:
Cakera pengisaran adalah penting dalam sektor automotif untuk tugasan daripada alat mengasah kepada membentuk dan kemasan komponen logam. Mereka menyumbang kepada ketepatan dan kualiti bahagian automotif.
Industri kerja kayu:
Pekerja kayu menggunakan cakera pengisar untuk membentuk dan melicinkan permukaan kayu. Cakera ini berkesan dalam mengeluarkan bahan berlebihan, menapis bentuk, dan menyediakan kayu untuk kemasan selanjutnya.
Pembuatan Am:
Cakera pengisaran mencari aplikasi dalam pelbagai proses pembuatan di mana penyingkiran bahan yang tepat diperlukan, menyumbang kepada pengeluaran komponen berkualiti tinggi.
C. Isu Lazim Yang Dihadapi
Kehausan dan Lelasan Cakera:
Penggunaan berterusan boleh menyebabkan kehausan dan lelasan cakera pengisar, menjejaskan prestasinya. Pemeriksaan dan penggantian tetap diperlukan untuk mengekalkan kecekapan.
Terlalu panas:
Geseran yang berlebihan semasa penggunaan berpanjangan boleh menyebabkan terlalu panas, menjejaskan ketahanan cakera dan kualiti permukaan siap. Langkah penyejukan yang betul dan rehat berkala adalah penting.
Tersumbat:
Cakera pengisaran boleh mengumpul sisa bahan, mengurangkan keberkesanannya. Pembersihan kerap atau memilih cakera dengan ciri anti-penyumbatan membantu mengelakkan isu ini.
Getaran dan Getaran:
Ketidakseimbangan atau haus yang tidak sekata boleh mengakibatkan getaran atau goyah, menjejaskan kedua-dua kualiti kemasan dan keselamatan operasi. Pemasangan dan pengimbangan yang betul adalah kritikal.
Pemilihan Cakera Salah:
Memilih jenis cakera pengisaran yang salah untuk bahan atau aplikasi tertentu boleh menyebabkan ketidakcekapan dan potensi kerosakan. Pemilihan yang betul berdasarkan keserasian bahan adalah penting.
Memahami definisi, kepentingan dan potensi cabaran yang berkaitan dengan cakera pengisaran adalah penting untuk industri yang bergantung pada alat ini. Dengan menangani isu biasa dan memastikan penggunaan yang betul, industri boleh memaksimumkan keberkesanan cakera pengisaran dalam aplikasi masing-masing.
Haus dan Koyak pada Cakera Pengisaran
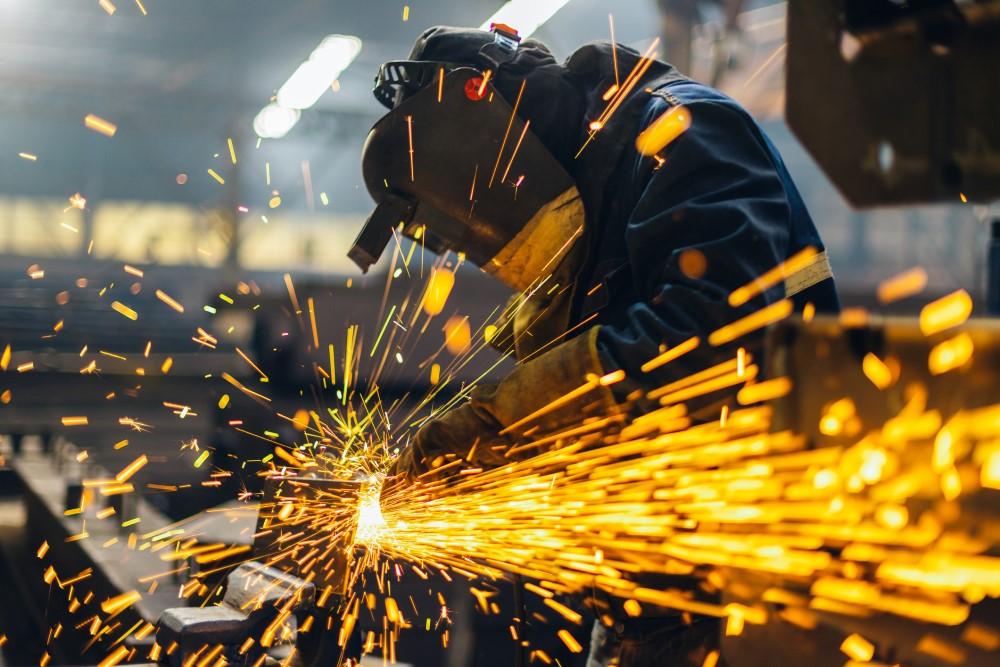
Cakera pengisaran ialah alat penting dalam pelbagai industri, menyediakan lelasan yang diperlukan untuk tugasan daripada fabrikasi logam kepada penggilap konkrit. Memahami faktor yang menyumbang kepada haus dan lusuh pada cakera pengisaran adalah penting untuk mengoptimumkan prestasinya dan memastikan keselamatan.
Kekerasan dan Komposisi Bahan:
Variasi kekerasan:Cakera pengisaran menemui bahan dengan tahap kekerasan yang berbeza-beza. Bahan pelelas seperti logam dan konkrit boleh berbeza dengan ketara dalam kekerasan. Pengisaran berterusan terhadap bahan keras mempercepatkan haus.
Komposisi Bahan:Kehadiran unsur pelelas dalam bahan yang dikisar boleh memberi kesan kepada kehausan pada cakera pengisar. Zarah pelelas boleh mempercepatkan kehausan cakera.
Tekanan dan Daya Pengisaran:
Tekanan Berlebihan:Mengenakan tekanan yang berlebihan pada cakera pengisar boleh menyebabkan haus yang lebih cepat. Adalah penting untuk menggunakan tekanan yang disyorkan untuk aplikasi khusus untuk mengelakkan ketegangan yang tidak perlu pada cakera.
Daya yang tidak mencukupi: Sebaliknya, daya yang tidak mencukupi boleh mengakibatkan pengisaran berpanjangan, menghasilkan geseran dan haba tambahan, menyumbang kepada haus.
Kualiti dan Komposisi Cakera:
Kualiti Bahan Pelelas:Kualiti bahan pelelas yang digunakan dalam cakera pengisar sangat mempengaruhi jangka hayatnya. Bahan pelelas berkualiti tinggi cenderung untuk menahan haus dan mengekalkan ketajaman lebih lama.
Ejen Ikatan:Ejen ikatan yang memegang zarah kasar bersama-sama memainkan peranan yang penting. Ejen ikatan yang direka dengan baik meningkatkan ketahanan cakera.
Keadaan Persekitaran Kerja:
Suhu:Suhu tinggi yang dijana semasa pengisaran boleh memberi kesan kepada komposisi cakera. Haba yang berlebihan melemahkan agen ikatan dan mempercepatkan haus.
Kelembapan dan Bahan cemar:Pendedahan kepada lembapan atau bahan cemar dalam persekitaran kerja boleh menjejaskan integriti cakera pengisar, yang membawa kepada haus yang lebih cepat.
Teknik Operator:
Teknik yang betul:Kemahiran dan teknik pengendali adalah penting. Penggunaan yang tidak betul, seperti mengisar pada sudut yang salah atau menggunakan daya yang berlebihan, boleh menyumbang kepada kehausan yang tidak sekata dan mengurangkan umur panjang cakera.
Pemeriksaan berkala:Operator harus kerap memeriksa cakera pengisar untuk sebarang tanda kerosakan atau haus. Cakera yang menunjukkan haus melebihi titik tertentu hendaklah diganti dengan segera.
Saiz Cakera dan Keserasian RPM:
Saiz yang betul:Menggunakan saiz cakera yang betul untuk pengisar adalah penting. Cakera bersaiz tidak betul mungkin haus tidak sekata atau menimbulkan risiko keselamatan.
Keserasian RPM:Mematuhi putaran seminit (RPM) yang disyorkan untuk cakera pengisaran memastikan prestasi optimum dan mengelakkan haus pramatang.
Penyelenggaraan tetap, pematuhan kepada keadaan operasi yang disyorkan, dan pemilihan cakera pengisar yang betul untuk tugas itu adalah amalan penting untuk meminimumkan haus dan lusuh. Dengan memahami faktor yang mempengaruhi haus, pengendali boleh meningkatkan umur panjang dan kecekapan cakera pengisaran, menyumbang kepada operasi pengisaran yang lebih selamat dan produktif.
Pengisaran Tidak Sekata
Pengisaran tidak rata merujuk kepada keadaan di mana permukaan yang dikisar tidak mencapai kemasan yang konsisten dan licin. Isu ini boleh timbul atas pelbagai sebab dan boleh memberi kesan kepada kualiti bahan kerja. Berikut ialah faktor biasa yang menyumbang kepada pengisaran tidak sekata dan penyelesaian yang berpotensi:
Pemilihan Roda Pengisaran yang Salah:
Penyelesaian:Pastikan roda pengisar sesuai untuk bahan yang dikisar. Bahan yang berbeza memerlukan sifat pelelas tertentu. Pilih jenis roda yang betul, saiz pasir dan ikatan untuk aplikasi.
Pembalut roda yang tidak betul:
Punca:Roda pengisar yang tidak berpakaian dengan betul boleh menyebabkan kehausan yang tidak sekata dan pemotongan yang tidak berkesan.
Penyelesaian:Kerap berpakaian roda pengisar untuk mengekalkan bentuknya dan keluarkan sebarang serpihan terkumpul. Pembalut yang betul memastikan permukaan pemotongan yang konsisten.
Cecair Pengisar atau Penyejuk yang Tidak Mencukupi:
Punca:Penggunaan cecair pengisar yang tidak mencukupi atau tidak betul boleh mengakibatkan peningkatan geseran dan haba, yang membawa kepada pengisaran tidak sekata.
Penyelesaian:Gunakan cecair pengisar atau penyejuk yang sesuai untuk menghilangkan haba dan mengurangkan geseran. Penyejukan yang betul adalah penting untuk mencapai hasil yang seragam.
Parameter Pengisaran Salah:
Punca:Menggunakan parameter pengisaran yang salah seperti kelajuan yang berlebihan, kadar suapan atau kedalaman pemotongan boleh menyebabkan pengisaran tidak sekata.
Penyelesaian:Laraskan parameter pengisaran mengikut keperluan bahan dan aplikasi. Rujuk kepada cadangan pengilang untuk tetapan optimum.
Roda Pengisar yang Haus:
Punca:Roda pengisar yang haus mungkin tidak memberikan permukaan pemotongan yang konsisten, mengakibatkan pengisaran tidak sekata.
Penyelesaian:Gantikan roda pengisar apabila ia mencapai penghujung hayatnya yang boleh digunakan. Periksa roda secara kerap untuk tanda-tanda haus.
Tekanan Tidak Sekata atau Kadar Suapan:
Punca:Tekanan yang tidak sekata atau kadar suapan yang tidak konsisten semasa mengisar boleh menyebabkan penyingkiran bahan yang tidak teratur.
Penyelesaian:Gunakan tekanan seragam dan kekalkan kadar suapan yang konsisten di seluruh bahan kerja. Kemahiran operator dan perhatian terhadap perincian adalah kritikal.
Isu Mesin:
Punca:Masalah mekanikal dengan mesin pengisar, seperti salah jajaran atau masalah dengan gelendong, boleh mengakibatkan pengisaran tidak sekata.
Penyelesaian:Lakukan pemeriksaan penyelenggaraan secara berkala pada mesin pengisar. Atasi sebarang isu mekanikal dengan segera untuk memastikan kefungsian yang betul.
Pemasangan bahan kerja:
Punca:Bahan kerja yang tidak selamat atau tidak sejajar boleh menyebabkan pengisaran tidak sekata.
Penyelesaian:Pastikan pelekapan dan penjajaran yang betul bagi bahan kerja. Lindunginya dengan ketat untuk mengelakkan pergerakan semasa proses mengisar.
Menangani pengisaran yang tidak sekata memerlukan gabungan persediaan peralatan yang betul, parameter operasi yang betul dan amalan penyelenggaraan tetap. Operator harus dilatih untuk mengenal pasti dan membetulkan isu dengan segera untuk mencapai hasil yang berkualiti tinggi dan konsisten dalam aplikasi pengisaran. Pemeriksaan yang kerap dan pematuhan kepada amalan terbaik menyumbang kepada penyingkiran bahan yang cekap dan seragam semasa proses pengisaran.
Masalah Terlalu Panas
Terlalu panas semasa mengisar adalah isu biasa yang boleh menjejaskan prestasi kedua-dua roda pengisar dan bahan kerja. Haba yang berlebihan boleh membawa kepada pelbagai masalah, termasuk hayat roda yang berkurangan, kerosakan haba pada bahan kerja dan kecekapan pengisaran yang berkurangan secara keseluruhan. Berikut ialah punca dan penyelesaian yang berpotensi untuk menangani masalah terlalu panas:
Parameter Pengisaran Salah:
Punca:Menggunakan parameter pengisaran yang tidak betul, seperti kelajuan berlebihan, kadar suapan atau kedalaman pemotongan, boleh menghasilkan haba berlebihan.
Penyelesaian:Laraskan parameter pengisaran dalam julat yang disyorkan. Rujuk garis panduan pengilang untuk tetapan optimum berdasarkan bahan yang dikisar.
Penyejukan atau Pelinciran yang Tidak Mencukupi:
Punca:Penggunaan cecair penyejuk atau pengisar yang tidak mencukupi boleh mengakibatkan peningkatan geseran dan haba.
Penyelesaian:Pastikan bekalan penyejuk atau pelincir mencukupi semasa proses pengisaran. Penyejukan yang betul membantu menghilangkan haba dan mengelakkan kerosakan haba.
Pemilihan Roda Salah:
Punca:Memilih roda pengisar dengan spesifikasi yang tidak sesuai untuk bahan yang dikisar boleh menyebabkan terlalu panas.
Penyelesaian:Pilih roda pengisar dengan jenis pelelas, saiz pasir dan ikatan yang betul untuk aplikasi khusus. Memadankan roda dengan bahan meminimumkan penjanaan haba.
Isu Bahan Bahan Kerja:
Punca:Sesetengah bahan, terutamanya yang mempunyai kekonduksian haba yang lemah, lebih terdedah kepada terlalu panas semasa mengisar.
Penyelesaian:Laraskan parameter pengisaran untuk bahan dengan kekonduksian terma yang lebih rendah. Pertimbangkan untuk menggunakan roda pengisar khusus yang direka untuk bahan sensitif haba.
Masalah Berpakaian Roda:
Punca:Penyelewengan atau pembalut yang tidak betul pada roda pengisar boleh menyebabkan sentuhan tidak sekata dan pembentukan haba.
Penyelesaian:Kerap berpakaian roda pengisar untuk mengekalkan bentuknya dan keluarkan sebarang kaca atau serpihan terkumpul. Roda berpakaian dengan betul memastikan prestasi pengisaran yang konsisten.
Penyelenggaraan Mesin yang Tidak Mencukupi:
Punca:Mesin pengisar yang tidak diselenggara dengan baik boleh menyumbang kepada isu terlalu panas.
Penyelesaian:Menjalankan penyelenggaraan berkala pada mesin pengisar, termasuk memeriksa sistem penyejuk, memeriksa peralatan pembalut roda, dan memastikan penjajaran yang betul. Atasi sebarang masalah mekanikal dengan segera.
Aliran Penyejuk Roda Tidak Mencukupi:
Punca:Aliran penyejuk yang tidak mencukupi ke zon pengisaran boleh mengakibatkan pelesapan haba berkurangan.
Penyelesaian:Semak dan optimumkan sistem penghantaran penyejuk. Pastikan penyejuk berkesan mencapai zon pengisaran untuk mengekalkan kecekapan penyejukan.
Masa Pengisaran Berlebihan:
Punca:Sesi pengisaran yang berpanjangan tanpa patah boleh menyumbang kepada pembentukan haba.
Penyelesaian:Laksanakan pengisaran berselang-seli dan biarkan rehat untuk mengelakkan pengumpulan haba yang berlebihan. Pendekatan ini amat penting untuk tugas pengisaran yang besar atau mencabar.
Menangani masalah terlalu panas dalam pengisaran memerlukan pendekatan komprehensif yang melibatkan persediaan peralatan yang betul, parameter pengisaran yang sesuai, dan amalan penyelenggaraan tetap. Operator harus memantau dan mengawal penjanaan haba semasa proses pengisaran untuk memastikan prestasi optimum, hayat alat yang dilanjutkan dan hasil yang berkualiti tinggi.
Kebimbangan Getaran
Getaran yang berlebihan semasa operasi pengisaran boleh membawa kepada pelbagai isu, termasuk kualiti permukaan yang berkurangan, peningkatan kehausan alat dan kemungkinan kerosakan pada mesin pengisar. Menangani kebimbangan getaran adalah penting untuk mencapai proses pengisaran yang tepat dan cekap. Berikut ialah punca dan penyelesaian yang berpotensi untuk mengurangkan masalah getaran:
Pakai Roda Tidak Sekata:
Punca:Haus yang tidak teratur pada roda pengisar boleh mengakibatkan sentuhan tidak sekata dengan bahan kerja, menyebabkan getaran.
Penyelesaian:Periksa dan gantikan roda pengisar secara kerap untuk mengekalkan permukaan yang konsisten dan rata. Penyelenggaraan roda yang betul membantu meminimumkan getaran.
Roda Pengisaran Tidak Seimbang:
Punca:Ketidakseimbangan dalam roda pengisar, sama ada disebabkan oleh haus yang tidak sekata atau kecacatan pembuatan, boleh menyebabkan getaran.
Penyelesaian:Imbangkan roda pengisar menggunakan pengimbang roda. Pengimbangan memastikan pengagihan berat yang sekata dan mengurangkan getaran semasa operasi.
Penentukuran Mesin yang Tidak Mencukupi:
Punca:Penentukuran yang lemah atau salah jajaran komponen mesin, seperti gelendong roda atau meja kerja, boleh menyumbang kepada getaran.
Penyelesaian:Kalibrasi dan selaraskan komponen mesin secara kerap untuk memastikan kefungsian yang betul. Ikuti garis panduan pengilang untuk persediaan dan penjajaran mesin.
Ketidakseimbangan bahan kerja:
Punca:Bahan kerja yang tidak rata atau tidak terjamin dengan betul boleh menimbulkan ketidakseimbangan dan menyebabkan getaran.
Penyelesaian:Selamatkan bahan kerja dengan betul, pastikan ia berada pada kedudukan yang sama dan diapit. Atasi sebarang isu ketidakseimbangan sebelum memulakan proses pengisaran.
Pemilihan Roda Salah:
Punca:Menggunakan roda pengisar dengan spesifikasi yang tidak sesuai boleh mengakibatkan getaran.
Penyelesaian:Pilih roda pengisar dengan jenis pelelas yang betul, saiz pasir dan ikatan untuk bahan yang dikisar. Memadankan roda dengan aplikasi meminimumkan getaran.
Haus dan Koyak Mesin:
Punca:Komponen mesin yang usang atau rosak, seperti galas atau gelendong, boleh menyumbang kepada getaran.
Penyelesaian:Selalu periksa dan ganti bahagian mesin yang haus. Penyelenggaraan yang betul membantu mengelakkan getaran yang berlebihan dan memanjangkan hayat mesin pengisar.
Aliran Penyejuk yang Tidak Mencukupi:
Punca:Aliran penyejuk yang tidak mencukupi ke zon pengisaran boleh mengakibatkan pembentukan haba dan getaran.
Penyelesaian:Optimumkan sistem penghantaran penyejuk untuk memastikan penyejukan yang betul. Penyejukan yang berkesan mengurangkan risiko pengembangan dan pengecutan haba, yang boleh menyebabkan getaran.
Isu Pemegang Alat:
Punca:Masalah dengan pemegang alat atau antara muka gelendong boleh menimbulkan getaran.
Penyelesaian:Pastikan pemegang alat dipasang dengan selamat dan dijajarkan dengan betul dengan gelendong. Gunakan pemegang alat yang berkualiti tinggi dan diselenggara dengan betul untuk meminimumkan getaran.
Asas Mesin:
Punca:Asas mesin yang lemah atau sokongan yang tidak mencukupi boleh menguatkan getaran.
Penyelesaian:Pastikan mesin pengisar dipasang pada asas yang stabil dan direka bentuk dengan betul. Atasi sebarang isu struktur untuk meminimumkan getaran yang dihantar ke mesin.
Menangani kebimbangan getaran dalam pengisaran secara berkesan memerlukan gabungan penyelenggaraan mesin yang betul, pemilihan roda dan pengendalian bahan kerja. Operator harus melaksanakan amalan pemeriksaan dan penyelenggaraan yang kerap untuk mengenal pasti dan menyelesaikan isu dengan segera, menghasilkan prestasi dan kualiti pengisaran yang lebih baik.
Memuatkan Isu dalam Pengisaran
Pemuatan dalam pengisaran merujuk kepada fenomena di mana ruang antara butiran kasar pada roda pengisar menjadi terisi dengan bahan yang dikisar, mengakibatkan tindakan pemotongan berkurangan dan peningkatan geseran. Pemuatan boleh memberi kesan negatif kepada kecekapan dan kualiti proses pengisaran. Berikut ialah punca dan penyelesaian yang berpotensi untuk menangani isu pemuatan:
Bahan Bahan Kerja Lembut:
Punca:Mengisar bahan lembut boleh menyebabkan tersumbat pantas bijirin kasar.
Penyelesaian:Gunakan roda pengisar dengan kersik yang lebih kasar dan struktur terbuka apabila bekerja pada bahan yang lebih lembut. Ini membantu menghalang pemuatan cepat dan membolehkan penyingkiran cip yang cekap.
Pencemaran Bahan:
Punca:Bahan cemar yang terdapat dalam bahan bahan kerja, seperti minyak, gris atau sisa penyejuk, boleh menyumbang kepada pemuatan.
Penyelesaian:Pastikan pembersihan bahan kerja dengan betul sebelum mengisar untuk menghilangkan bahan cemar. Gunakan cecair pemotong atau penyejuk yang sesuai untuk meminimumkan pemuatan.
Aplikasi Penyejuk yang salah:
Punca:Penggunaan penyejuk yang tidak mencukupi atau tidak betul boleh menyebabkan pelinciran dan penyejukan yang tidak mencukupi, mengakibatkan pemuatan.
Penyelesaian:Optimumkan aliran penyejuk dan kepekatan. Pastikan penyejuk berkesan mencapai zon pengisaran untuk melincirkan dan menyejukkan proses, menghalang pemuatan.
Ketajaman Roda Tidak Mencukupi:
Punca:Roda pengisar yang kusam atau usang lebih terdedah kepada pemuatan kerana ia kehilangan kecekapan pemotongan.
Penyelesaian:Kerap berpakaian dan mengasah roda pengisar untuk mengekalkan ketajamannya. Gunakan almari roda untuk mendedahkan butiran kasar yang segar dan meningkatkan tindakan pemotongan.
Kelajuan Roda Rendah:
Punca:Mengendalikan roda pengisar pada kelajuan rendah mungkin tidak memberikan daya emparan yang mencukupi untuk mengeluarkan cip, yang membawa kepada pemuatan.
Penyelesaian:Pastikan mesin pengisar beroperasi pada kelajuan yang disyorkan untuk gabungan roda dan bahan kerja tertentu. Kelajuan yang lebih tinggi boleh membantu dalam penyingkiran cip yang lebih baik.
Tekanan Berlebihan:
Punca:Menekan terlalu banyak tekanan semasa mengisar boleh memaksa bahan masuk ke dalam roda, menyebabkan pemuatan.
Penyelesaian:Gunakan tekanan pengisaran sederhana dan konsisten. Laraskan kadar suapan untuk membolehkan roda memotong dengan cekap tanpa tekanan berlebihan yang membawa kepada pemuatan.
Spesifikasi Roda Salah:
Punca:Menggunakan roda pengisar dengan spesifikasi yang salah untuk bahan yang dikisar boleh mengakibatkan pemuatan.
Penyelesaian:Pilih roda pengisar dengan jenis pelelas, saiz pasir dan ikatan yang sesuai untuk aplikasi khusus. Memadankan roda dengan bahan membantu mengelakkan pemuatan.
Pembersihan Bahan Penyejuk yang Tidak Mencukupi:
Punca:Bahan penyejuk yang tercemar atau lama mungkin menyumbang kepada isu pemuatan.
Penyelesaian:Bersihkan dan gantikan penyejuk secara kerap untuk mengelakkan pengumpulan bahan cemar. Penyejuk yang segar dan bersih meningkatkan pelinciran dan penyejukan, mengurangkan kemungkinan pemuatan.
Teknik Berpakaian yang Tidak Betul:
Punca:Pembalut yang salah pada roda pengisar boleh menyebabkan penyelewengan dan pemuatan.
Penyelesaian:Pakai roda dengan betul menggunakan alat pembalut yang sesuai. Pastikan profil roda adalah konsisten dan bebas daripada penyelewengan untuk mengelakkan pemuatan.
Menangani isu pemuatan secara berkesan melibatkan gabungan pemilihan roda yang betul, persediaan mesin dan amalan penyelenggaraan. Operator harus mengikut prosedur yang disyorkan, menggunakan parameter pengisaran yang sesuai, dan melaksanakan pembalut roda biasa untuk meminimumkan pemuatan dan mengoptimumkan prestasi pengisaran.
Memilih cakera pengisaran yang betul adalah penting untuk mencapai hasil yang optimum dalam pelbagai aplikasi kerja logam dan fabrikasi. Pemilihan bergantung pada faktor seperti bahan yang sedang diusahakan, kemasan yang diingini, dan jenis pengisar yang digunakan.
Memilih Cakera Pengisar yang Betul
Keserasian Bahan:
Logam Ferus (Keluli, Besi):Gunakan cakera pengisar yang direka khusus untuk logam ferus. Cakera ini selalunya mengandungi bahan pelelas yang sesuai untuk kekerasan keluli dan kurang terdedah kepada pemuatan.
Logam Bukan Ferus (Aluminium, Loyang):Pilih cakera dengan bahan pelelas yang sesuai untuk logam yang lebih lembut untuk mengelakkan tersumbat. Cakera aluminium oksida atau silikon karbida adalah pilihan biasa.
Bahan pelelas:
Aluminium Oksida:Sesuai untuk tujuan umum pengisaran pada logam ferus. Ia tahan lama dan serba boleh.
Zirkonia Alumina:Menawarkan kecekapan pemotongan yang lebih tinggi dan tahan lama, menjadikannya sesuai untuk pengisaran agresif pada logam ferus dan bukan ferus.
Silicon Carbide:Ideal untuk mengisar logam dan batu bukan ferus. Ia lebih tajam tetapi kurang tahan lama daripada aluminium oksida.
Saiz Grit:
Pasir Kasar (24-36):Pembuangan stok pantas dan pengisaran tugas berat.
Grit Sederhana (40-60):Mengimbangi penyingkiran stok dan kemasan permukaan.
Grit Halus (80-120):Menyediakan kemasan licin, sesuai untuk penyediaan permukaan dan pengisaran ringan.
Jenis Roda:
Jenis 27 (Pusat Tertekan):Cakera pengisaran standard dengan permukaan rata, sesuai untuk pengisaran permukaan dan kerja tepi.
Jenis 29 (Kon):Reka bentuk bersudut untuk penyingkiran stok yang agresif dan pengadunan permukaan yang lebih baik.
Jenis 1 (Lurus):Digunakan untuk aplikasi cut-off. Ia menyediakan profil nipis untuk pemotongan yang tepat.
Permohonan:
Pengisaran:Cakera pengisaran standard untuk penyingkiran dan pembentukan bahan.
Memotong:Gunakan roda pemotong untuk memotong logam, memberikan tepi yang lurus dan bersih.
Cakera Kepak:Gabungkan pengisaran dan penamat dalam satu. Sesuai untuk mengadun dan menghaluskan permukaan.
Keserasian dengan Pengisar:
Pastikan cakera pengisar serasi dengan jenis dan kelajuan pengisar yang digunakan. Semak cadangan pengilang untuk RPM maksimum (Putaran Per Minit) cakera.
Kekhususan Tugas:
Penyingkiran Stok Berat:Pilih kersik kasar dan cakera jenis 27 atau jenis 29 untuk penyingkiran bahan yang cekap.
Kemasan Permukaan:Pilih grits sederhana hingga halus dengan cakera flap untuk kemasan yang lebih licin.
Pertimbangan Keselamatan:
Ikut garis panduan keselamatan, termasuk memakai peralatan pelindung diri (PPE) yang sesuai seperti cermin mata dan sarung tangan keselamatan.
Pilih cakera bertetulang untuk ketahanan dan keselamatan tambahan.
Jenama dan Kualiti:
Pilih cakera daripada jenama terkenal yang terkenal dengan kualiti dan konsistensi. Cakera berkualiti tinggi menawarkan prestasi dan ketahanan yang lebih baik.
Pertimbangan Kos:
Seimbangkan kos awal dengan jangka hayat dan prestasi cakera pengisar yang dijangkakan. Cakera berkualiti tinggi mungkin mempunyai kos pendahuluan yang lebih tinggi tetapi boleh memberikan nilai yang lebih baik dari semasa ke semasa.
Dengan mempertimbangkan faktor-faktor ini, pengendali boleh memilih cakera pengisaran yang betul untuk aplikasi khusus mereka, memastikan kecekapan, keselamatan dan hasil yang optimum.
Kesimpulan
Kesimpulannya, memilih cakera pengisaran yang sesuai adalah aspek kritikal untuk mencapai hasil kerja logam dan fabrikasi yang berjaya. Pilihan bergantung pada pelbagai faktor seperti bahan yang sedang diusahakan, kemasan yang diingini, dan jenis pengisar yang digunakan. Dengan mempertimbangkan keserasian bahan, jenis pelelas, saiz pasir, jenis roda, aplikasi, keserasian pengisar, kekhususan tugas, keselamatan, kualiti jenama dan kos, pengendali boleh membuat keputusan termaklum untuk meningkatkan kecekapan dan keselamatan dalam proses pengisaran mereka.
Adalah penting untuk mematuhi garis panduan keselamatan, memakai peralatan pelindung diri yang sesuai, dan mengikut saranan pengilang untuk keserasian pengisar dan cakera. Sama ada untuk penyingkiran stok berat, kemasan permukaan atau aplikasi pemotongan, cakera pengisar yang betul boleh memberi kesan ketara kepada kualiti dan kecekapan kerja.
Selain itu, pemeriksaan berkala untuk haus dan lusuh, menangani isu seperti kepanasan melampau dan kebimbangan getaran, dan memahami masalah pemuatan menyumbang kepada memanjangkan hayat cakera pengisaran dan memastikan prestasi yang konsisten.
Ringkasnya, pendekatan yang bermaklumat dan sistematik untuk memilih, menggunakan dan menyelenggara cakera pengisaran adalah kunci untuk mencapai hasil yang optimum, meningkatkan produktiviti dan memastikan persekitaran kerja yang selamat.
Masa siaran: Jan-12-2024